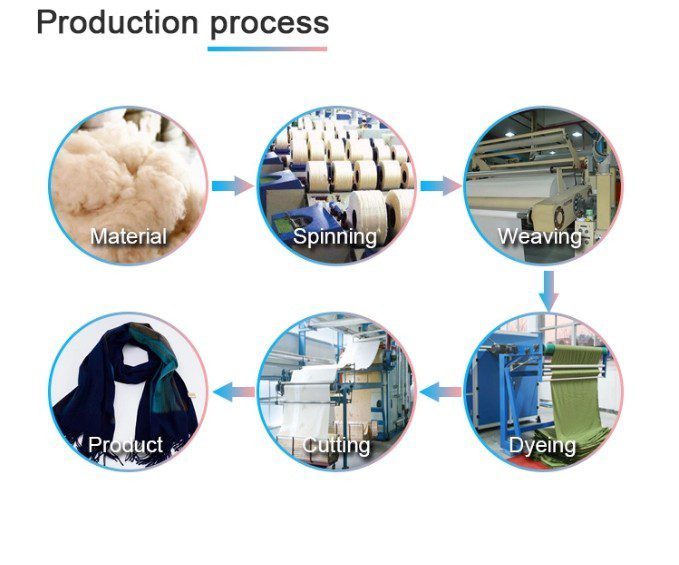
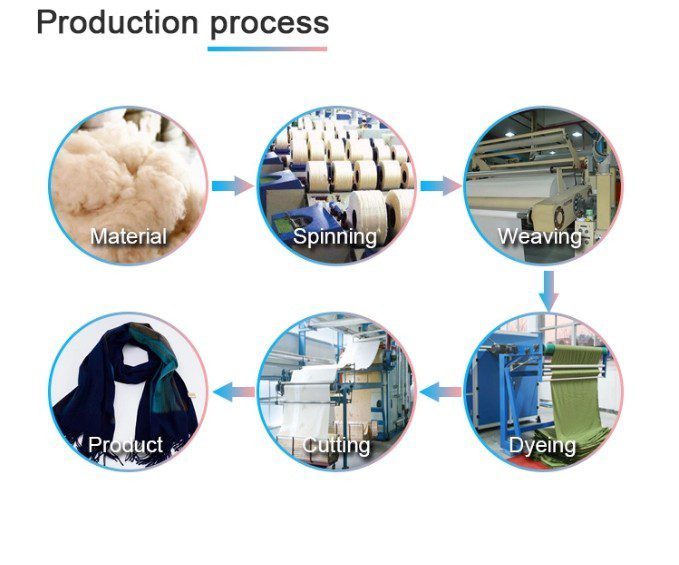
1. WHAT’S A SCARF
SCARF PRODUCT DEFINITION: SCARF PRODUCTS CAN be divided into: SCARF, Shawl, scarf, veil and so on by material can be divided into: Silk Scarf, knitted scarf, acrylic scarf, linen scarf, wool scarf, cashmere scarf, velvet blend scarf, etc. .
2. PRESENT SITUATION AND DEVELOPMENT PROSPECT OF SCARF INDUSTRY
SCARF, hat and gloves industry entry threshold is low, small-scale enterprises, extensive management, products mainly rely on large quantities of cheap occupy the market, marketing concept is missing; in addition, factors such as the lack of international famous brands and the price of raw materials have seriously restricted the further development of the industry and the improvement of its quality In the personalized, the diversification of production on the full effort to change the situation of low-priced exports. In the same technology, the same raw materials, the same equipment conditions, the same level of management, the enterprise has been from the original product quality competition, to spell personality, service. To be able to do the elements of brand success in place, the ultimate is the brand value of the struggle. We should constantly launch famous brand products, create value chain marketing, realize the combination of culture and technology, only in this way can we be invincible in the new situation.
3. SCARF INDUSTRY BUYERS FOCUS
WORLD SCARF TREND
Natural environmental products lead to draw design inspiration from nature, becoming the trend of scarf. A variety of healthy, comfortable environment-friendly fabrics, through weaving, printing, Jacquard, embroidery, laser carving and other forms of interpretation, showing endless changes and visual enjoyment. Made of natural materials such as hemp, cotton, wool and silk, the scarf is breathable, soft, firm, elegant and warm Its sales prospect is very broad 2) the style is changeable manifests the unique charm. Women of different temperament can be matched with different styles of scarves, such as neck-style scarf with youth, scarf with a scarf scarf scarf, noble and elegant; hoodie-style scarf with casual casual evening dress, half-length skirt-style scarf with a variety of styles, let you suddenly become fashionable people,) the use of a wide range of popular market. The use of scarf has long been from the traditional sense of warmth to a variety of fashion, decorative and leisure features, fashion scarf collocation and innovative function to bring us eyes-new feeling. Can Be used as a headdress, braided together with the Braid; as a necklace and accessories to match-up; as a belt twisted into a twist tied to the waist; or as an ornament, tied into a rose, bow and other shapes, hanging on the bag, a versatile, creative.
4. China is a major exporter of scarves
The main export countries of knitted scarf are the United States, Germany, Britain, South Korea, Italy and other countries, among which the sports style of knitted scarf is mainly exported to Europe and other countries where football clubs are flourishing, and the trend of export is rising significantly. Synthetic scarves are mainly exported to the United Arab Emirates, the United States, Russia and other countries, including Rayon, Rayon and other materials, with strong and durable, easy to wash and dry, cost-effective advantages, but there are also many disadvantages Such as poor thermal insulation, easy to electrify fuzzing and so on. But these shortcomings are being constantly overcome, water-absorbing fiber, heat-resistant fiber and other colored fibers have come out one after another.
5. Buyer’s focus in scarf industry — Characteristics of buyer’s purchasing in North America
In the communication with the buyer, never talk about the depth, or in the negotiation process with the buyer encounter conflict. These problems boil down to a lack of assurance about the characteristics and real needs of different buyers. Today I would like to introduce to you the characteristics of American buyers, the main export market for scarves I hope to help you communicate with the buyer more effectively the characteristics of North American overseas buyers and the way to deal with: 1, the treatment of specific business, contract will be very cautious, pay attention to publicity and appearance. American businessmen not only attach importance to the quality of national towel, but also attach importance to the packaging of national towel products 2, attach importance to efficiency, value time, pursue realistic interests, attach importance to publicity and appearance. U. S. negotiators value the efficiency of the inquiry response, like a quick fix, if the inquiry response process to provide the active service, buyers will be impressed with such sellers. When negotiating or quoting to American buyers, special attention should be paid to the whole, to the whole, to the whole, to the whole, to the whole, to the whole, to the whole. Those who are good at expressing sincere feelings directly to the other party are also easy to infect others. We should make full use of them and encourage them accordingly in order to create a good negotiation atmosphere and create a chance of success.Is this a common problem in finding scarf suppliers?There are several common problems when looking for a scarf supplier.
1. RISING COSTS
With the rise in prices, the production cost of scarf products has further increased, if the cost control quality and design can not be guaranteed, and Sagemoda, as an advanced enterprise with many years of production experience, has become the responsibility to help customers reduce costs According to the customer selection of fabric production, the links to minimize customer costs.
2. LACK OF DESIGN
With the continuous improvement of brand awareness in the market, more and more scarf buyers pay attention to the design of their own products, but for various reasons product design has become a major problem for buyers. Sagemoda, as the ODM scarf supplier, has a strong product design team to meet all kinds of customer design needs.
3. Long Shipping Cycle
The cycle of delivery determines the response of the scarf in the market. If the rapid delivery speed, the buyer’s products will better grasp the market trend, get more market share. SAGEMODA adopts the latest production cycle system and can monitor the whole production process to ensure the customer’s delivery cycle is greatly shortened.
4. Quality Not Guaranteed
Quality is the most important of all foreign trade enterprises, quality is not guaranteed will cause great losses to buyers. SAGEMODA has adopted the world-leading quality inspection technology
to ensure the quality of customers’products can stand the test of the market after many well-known brand buyers’experiences.
Six major issues of textile industry in 2015
In the new normal, this year, the textile industry has taken on new characteristics. First, growth in high-speed, production, exports, investment, domestic sales, PROFITS
The growth rate of various operational indicators such as the previous few years slowed down, since June has ended the previous monthly pick-up trend, the second half of this year has shown more obvious reduction
Speed situation, the industry in the annual slowdown into the normal economic growth, while further in-depth promotion of transformation and upgrading is still facing greater pressure. The second is the Spear
Shield, difficulties and challenges increased, the domestic cotton market situation complex, domestic demand market growth significantly slowed down, the overall cost continued to rise, international competition more
A series of severe challenges remain to be resolved, the industry’s own raw materials, production capacity, layout, enterprise organization and other aspects of the inherent structural contradictionsThat needs to be addressed.
From the whole year, the macro environment at home and abroad is basically stable, market fundamentals have not deteriorated significantly, the country’s steady growth, restructuring, Huimin County
Health, risk related Macroeconomic regulation and control policies are generally beneficial to the industry. But the textile industry to continue to maintain a smooth operation situation, still need to effectively resolve the risk of contradictions, to speed up its own transformation and upgrading is still the fundamental task of development.
Textile Industry in the development of various external risks and internal contradictions to accelerate the transformation and upgrading of the industry put forward specific direction and task requirements. The current industry needs to focus on the issue of the main performance of the following six areas.
Domestic cotton market and COTTON SITUATION IS STILL COMPLEX
In 2014, domestic and foreign cotton price gap is still large, and the situation of domestic cotton is complex. Domestic cotton management policy to achieve a new breakthrough for the new listing
Xinjiang cotton, the state has decided to give planting subsidies according to the difference between the average market price and the target price from September to November, which will be conducive to the gradual recovery of the country
Market attribute of inner cotton price. However, due to the direct subsidy policy implementation effect is still uncertain, national cotton storage, import quotas and other policies for domestic cotton
Price will also have a direct impact on the overall situation of the domestic cotton market more complex. Cotton and downstream product prices continued to be in the downward range, also increased
In order to manage the risk, more test the market reaction and internal management ability of the textile enterprise, the influence of the cotton problem on the smooth operation of the textile
industry can not be ignored.
The task of chemical fiber production capacity structure adjustment is arduous
In 2013, China imported 4.15 million tons of cotton, accounting for about 40 percent of the annual cotton consumption, with a cumulative import of 2.1 million tons of cotton yarn, an increase of 37 percent year-on-year
Former cotton spinning enterprise non-cotton fiber processing accounted for 65% . Since last year, domestic PTA and polyester, polyester and other chemical fiber raw materials and products prices continued
Trend, enterprise loss pressure increased, chemical fiber industry production capacity staged, structural surplus, market excessive competition is an important reason.
The chemical fiber raw material development lags behind the product development, and the raw material external dependence degree is high, 2013 China PX, MEG external dependence degree reached 52.8%,69.87% , of which PX due to environmental safety and social issues almost stagnant development, obvious bottleneck constraints on raw materials, in 2013 China imported px90478Tons, up 43.93 percent year on year.
From May to July this year, the backbone PTA enterprises have made some progress by strengthening self-discipline, reducing output and standardizing competition order. But how to keep it that way
Self-discipline and market order, how to effectively downstream industries and the normal transmission of raw material price fluctuations and other issues, still need to strengthen attention and research. In the meantime,around the market terminal demand, further enhance the functionality of fiber, differential level, and actively develop new varieties of chemical fiber, is to resolve the production capacity structure
It is an urgent and long-term task for the industry to solve the contradiction between supply and demand of cotton and other textile materials and to promote the structural adjustment of the industry.
The pressure of energy conservation and environmental protection constraints increased
Textile Industry is facing the pressure of higher emission standards than developed countries and regions, especially from the domestic and international environmental organizations
Public opinion pressure, and increasingly stringent industry access, land, financing restrictions pressure. During this year’s two sessions, Premier Li Keqiang called for a resolute crackdown on corruption
The declaration of war further strengthened the country’s determination and position on energy conservation and environmental protection. Government departments at all levels constantly raise standards for the supervision and control of pollutant discharge
Increase the scope of supervision, administrative law enforcement efforts to strengthen. Air Pollutant emission standards for textile printing and dyeing industry will be issued soon, further increasing the industry
Environmental mission pressure. Various standards do not set a transitional period, the total
amount of pollutants emission reduction heavy and other objective circumstances, and the vast number of small and medium-sized textile enterprises
Limited ability to cope with the conflict, the industry is in urgent need of funds, technology inputs and management experience, public services and other support to enhance the capacity for sustainable development.
The adjustment of industrial distribution faces new situation and new problems
The adjustment of industrial distribution faces new situation and new problems as follows: First, the pace of undertaking the transfer of textile industry in central China continues to slow down
In the first eight months of this year, the total investment in the industry fell by 0.2 percentage points compared with the same period last year
Obstacle. To give full play to the role of the central region in the domestic distribution system, further in-depth investigation and study are needed to put forward policies and measures
Xinjiang has gradually become a new hot spot for domestic textile industry investment, but it needs to strengthen planning guidance and realize the organic combination of industrial development and resources and environment conditions
, In line with the requirements of long-term social stability, rational allocation of industrial structure, to avoid over-expansion of local links in the industrial chain, reduce development efficiency;
In addition to improving in-depth research on the investment environment of foreign countries, developed countries are participating in the development of the international distribution of the Industry
Regional Free Trade Agreement on the impact of the global industrial layout is deepening, the industry should also take full account of this impact factor, early study of countermeasures.
The survival and development of small and medium-sized enterprises are under great pressure
In recent years, domestic raw materials, labor and other factors, as well as financing, channels and other costs continue to increase, the pressure to increase the overall cost is very sudden
Come out. Take the labor cost as an example, labor cost continued to rise, the rate of increase has decreased compared to the same period last year, in the first half of the year, migrant labor force monthly average
Incomes rose 10.3 percent, and 16 regions have adjusted their minimum wages this year, with an average increase of 14.2 percent, according to the Ministry of Social Security. Subject to capital
The strength of gold, technology, talents and management is limited. The ability of the vast number of small, medium-sized and micro enterprises to enhance their development is obviously insufficient, and the adjustment they face is even more severe
The survival dilemma is becoming more and more obvious. In view of the characteristics of small and medium-sized micro-enterprises, a series of work, such as research on policy support measures and strengthening public service support, should be strengthened urgently.
World Cup fan scarves push foreign trade orders With the World Cup approaching, foreign trade scarf orders have also increased. This World Cup trade will give many scarf manufacturers a very large production period. ODM , a supplier based in Suzhou, also received a large number of foreign trade orders ahead of the World Cup.
The World Cup is a test for soccer players from all over the world. It is also a test for the production and design ability of scarf manufacturers.
What should we pay attention to when ORDERING FOREIGN TRADE SCARF
SCARF MANUFACTURERS DO foreign trade scarf order is not an easy thing, to do well, must start from the following aspects: style, quality (dyeing, printing) , after the packaging, delivery.
1. STYLE: Before receiving foreign trade orders, may give foreign customers a choice of style, pattern, so style is very important, pattern to be fashionable and unique, to suit the taste of foreigners. Color collocation: foreign customers like a bit of color, to master the current popular color.
2, quality: Dyeing Printing Quality, dyeing strictly in accordance with the color number provided by customers, color fastness to reach the standard, printing can not have color, white (except special style) ;
3, delivery time: strictly in accordance with the guests designated time delivery, because the guests have a fixed schedule, flights, if delayed, light deduction, heavy can not deliver, this is taboo, and must ensure the number of shipments, can not be short;
4, after the road packaging should also be strictly checked;
Scarf factory pay attention to these things, will be able to grasp the psychology of domestic and foreign customers, scarf wholesalers will also come to you here for procurement.
Silk scarves could become the centerpiece of the SCARF INDUSTRY
Recently, many people are discussing the market share of various types of scarves, from the perspective of foreign trade scarf manufacturers, silk to become the main event still need time.
In recent years, silk scarf began to emerge in the domestic scarf industry, and quickly by virtue of
exquisite workmanship, novel style has been sought after by consumers, the scarf industry has become a hot-selling products.
With the gradual popularity of silk scarves, China’s silk scarf industry is also rapidly developing. In the next three to five years, silk scarves are expected to surpass the traditional scarf industry, according to operators specializing in the production and sale of silk scarves in China.
With the change of people’s life concept and consumption habits, the traditional scarves with the main function of keeping out the cold gradually fade out of people’s vision, and the fashionable, exquisite, elegant and noble silk scarves became popular The market volume of this product will also increase year by year. Silk Scarf in the future development of the scarf industry will become the highlight, and is expected to surpass the traditional scarf industry.
What are the manufacturing processes adopted by foreign trade scarf manufacturers?
What does foreign trade scarf craft have? SCARF technology mainly includes: printing technology, yarn-dyed technology, Jacquard Technology, hand-painted technology, tie-dyeing technology. General scarf wholesale manufacturers will cover these production processes.
Printing process is the process of printing patterns on textile fabrics with dyes or pigments.
Yarn-dyed process: A process in which yarn or filament is dyed and then colored yarn is used for Weaving.
Jacquard process: WEAVING PROCESS OF TEXTILE FABRICS TO WARP and weft interlaced composition of the concave-convex pattern.
Hand-painted craft: is the scarf is originally a plain color of a piece of fabric, with watercolor painting above, and then use chemical solid color scarf. The scarf is distinctive and special, and can be used as you wish.
TIE-DYEING PROCESS: tie-dyeing is a traditional and unique dyeing process in China. A dyeing method in which the fabric is partially tied up so that it can not be dyed. It is one of the traditional Chinese techniques of hand dyeing.
SCARF manufacturers are printing process and hand-painted process as their main technology,
which is also relatively mature production process, general manufacturers will meet customer needs.
TIE-DYEING PROCESS OF FOREIGN TRADE SCARF
Tie-dyeing process is the most widely used in the production of wool and cashmere scarves by scarf manufacturers. tie-dyeing process is the most skilled process in scarf factories. The following and Sageoda together to learn about the tie-dye technology in foreign trade scarves.
Tie-dyed products are printed rather than printed and are a form of local dyeing. Tie-dye out of the pattern, spontaneous, diverse patterns, fresh colors, rich colors. And because the pattern pattern in the tone of its big style, will not produce mechanical complete repetition, so tie-dyed scarf, each one is a personalized single article.
Tie-dye process brief description:
Tie-dyeing technology is mainly divided into two key links: tie-dyeing and dyeing. The former part is called “tie” , but the actual operation can be divided into a variety of folding, folding, stranding, button, sewing, binding, and so on. The latter part is called “dyeing” , and there are pre-treatment, dyeing, finishing and other three stages of the process.
From the point of view of technology, tie-dyeing products today are not entirely traditional handicraft products, but highly combined with modern dyeing and finishing technology. Because of the particularity of tie-dye’s “tie-dye” process, there are subtle differences in manual operation, and the patterns that come out are unique and never identical, so there is no possibility of “matching shirts” Also greatly satisfied the current consumer pursuit of “unique” psychology.
As a result of scarf wholesale on wool, cashmere scarf demand is growing, tie-dyeing process month more mature.
Different scarf textures require different ironing methods
SCARF manufacturers all make different kinds of scarves, but consumers know very little about how to iron and clean their own scarves. Today, Sagemoda takes you to find out what kind of ironing is required for different kinds of scarves.
The silk is pressed dry on medium heat. Iron the corners of the scarf with the front end of the iron, then slide it out from the middle, stretching it flat.
Pure wool is steamed at medium temperature. Press gently on the scarf when ironing, do not press too hard, so as not to crush the hair.
Low temperature steam ironing for Chiffon. All you have to do is iron out the folds of the scarf.
In the ironing method, each scarf manufacturer is very similar, including foreign trade scarf manufacturers in ironing more attention.
IMPORTANCE OF INTERNAL CONTROL IN FOREIGN TRADE SCARF FACTORY
From a global perspective, strengthening the construction of internal control in foreign trade scarf factories has become a trend. Among them, the United States, the United Kingdom is an early concern about foreign trade scarf factory internal control countries, its foreign trade scarf factory internal control framework is also relatively sound and perfect.
In the United States, for example, from 1948, when the GAO proposed that “proper internal control is an integral part of the accounting system of federal agencies” , to 2008, the U.S. Congress enacted the Inspector General Reform Act
The Internal Control Construction Act, which further strengthens the independence of the inspector general, has undergone more than half a century of reform, and the internal control framework of the foreign trade scarf factory has been basically established and gradually improved. Among the most influential were the 2004 revision of the General Budget Administration’s (Omb) notice on management’s responsibility for internal control and the new risk-and performance-based federal government internal control guidelines issued by the United States General Audit Office (Gao) in 1999. Of course, this period also saw the publication how to
evaluate and improve internal controls in foreign trade scarf factories by Irwin David and Eugene Sturgeon (1981) , and the publication of internal controls in local governments: A guide for government officials by Mark Dirsmith and Abraham Simon (1983) However, its influence is not as powerful as the promotion and influence of the regulators on the internal control of foreign trade scarf factories.
Of course, in addition to the U. S. regulators on the government’s internal control of concern and research, other international organizations also on the government’s internal control of a strong concern.
In 2001, the International Federation of Accountants published a Management Perspective on public sector governance, providing governments with the best examples of governance, highlighting the idea of internal control.
In 2004, the International Organization of Supreme Audit Institutions (Intosai) was absorbing Co..
On the basis of the integrated framework of enterprise risk management published by SO, and in combination with the characteristics of public sector management, “Risk Assessment” has been added to the guidelines for internal control in the public sector. This paper explains the relationship between risk management and internal control, emphasizes the importance of risk assessment of foreign trade scarf factory, and standardizes how to carry out risk assessment in public sector. In addition, INTOSAI proposes an optimal governance structure for a foreign trade scarf factory consisting of a code of conduct, organizational structure and procedures, control activities and external reporting, and that strengthened internal controls should be a key element for good governance.
The role of precise management of PRODUCTION EQUIPMENT IN SCARF FACTORY
SCARF manufacturers have set up automatic equipment management systems with the functions of Planning Management, information collection, statistical analysis, quality evaluation, and so on
The utility model reduces the man-made nature and the randomness, and realizes the goal of efficient and economical equipment management. From the formal point of view, the equipment management of scarf manufacturer has the function of standardizing and restraining the behavior of the manager, meanwhile, it should exert the function of equipment management in arousing the enthusiasm, initiative and creativity of people. In order to carry out precise management, the guiding ideology of scarf manufacturers includes establishing and perfecting incentive mechanism, maximizing the potential of equipment management object and improving the benefit of equipment management. SCARF manufacturers make full use of information technology to objectively and accurately evaluate the performance of the equipment management object, according to which the rewards and punishments, effectively mobilize the management object’s inherent enthusiasm and initiative.
SCARF FACTORY equipment management out of efficiency, accurate management out of high efficiency. The standardized level of equipment management of scarf manufacturers has been improved. The prominent function of equipment management is to use rules and regulations to regulate the behavior of the regulated, and to maintain good work and production order. Because of the limitation of traditional equipment management, it is difficult to monitor and control the equipment management object all the time and the efficiency of equipment management is low. The implementation of precise management, relying on network technology, the application of modern information technology means to eliminate the equipment management blind area, reduce the occurrence of accidents, improve the standard construction level.
The systematicness of equipment management of scarf manufacturers is improved. The development of modern equipment has tended to multi-level and multi-type complex structure, forming a huge system. To carry out precise management is to meet the needs of modern equipment management and to improve the systematic level of equipment management. In accordance with the principle of accurate management of standard plus management and relying on advanced information technology, we have realized the transparent management of the whole process of material acquisition, storage, transportation, distribution and use, thus saving funds to the maximum extent To ensure the accuracy of the direction and amount of funds and materials invested, to track the use of funds through the network, to strengthen supervision, to eliminate loopholes in the management of equipment, and to achieve the optimization of the use efficiency of funds and materials, finally, the demand of personalized service is realized.
What measures are there for production management of high-grade SCARF MANUFACTURERS
Strengthening quality management from improving product quality. In view of the insufficiency of the current product quality and the customer demand, the director of the high-grade scarf manufacturer should actively cooperate with the technical department from the equipment, the operation, the craft to look for the reason, looks for the problem, strengthens the quality responsibility system the examination and the implementation, the index and quantity index is divided into teams, individuals and linked with economic responsibility system to improve and stabilize product quality. The high-grade scarf manufacturers have established and implemented the total quality management mode in the quality management: That is, the four production stages of the whole production process, namely, the formation of the production plan, the input, the production and the finished product, are all brought into the quality control system Integrate it into a tightly linked quality management system.
To strengthen quality management, we should also strengthen the comprehensive management of personnel in enterprises, the quality of employees and the level of production skills directly affect the quality of work and the quality of products. We should strengthen the education and training of employees so as to enhance their combat effectiveness So that it can meet the needs of production and technological progress, and strive to achieve “as soon as called, to be able to fight, battle to win. “.
It is very important to strengthen equipment management, make rational use of the existing equipment of high-grade scarf factory, and make the existing equipment give full play to its working efficiency. We should know that the rational use of equipment and increase the utilization rate of equipment will reduce the cost of products and increase the service life of equipment. We should arrange the staff according to the characteristics of equipment and the
capacity of Equipment To let the operator can not be brutal operation and overload work, that is to say, according to the equipment operating procedures and equipment maintenance system to use our equipment, in a real sense to improve the utilization of equipment. At the same time, strengthen the daily maintenance of equipment, establish and standardize the maintenance system, so that the production equipment has always maintained a good working condition; To make it better serve the safety of production and scientific research in enterprises.
Strengthening the construction of teams and groups from improving the quality of team leaders. Team leader in the high-grade scarf manufacturers throughout the operation of its importance is not to be underestimated. Team is the cell of enterprise, is the most basic unit of Labor Organization. Strengthening the construction of teams and groups, giving full play to the role of the backbone of teams and groups is the focus of management work of high-grade scarf manufacturers. Therefore, in our work, we should communicate more with the team leaders and strive to create a relaxed and happy working atmosphere. We should link responsibility, power and interests with the team leaders, so that we can have responsibility and power, and fully mobilize the enthusiasm and creativity of the team leaders At the same time, we should strengthen the training of team leaders’own ability, create conditions, provide a stage for them to exert their intelligence and talent, and create a team of team leaders who have talent, fine business and understand technology. In addition, to improve the technical level of workers. “The creation creates the person first” , the Worker’s technical quality and the product quality are closely related. The high-grade scarf manufacturers are earnestly focusing on the construction of the technical quality of the staff and workers, strengthening the training of professional skills and operational techniques, improving the staff and workers’professional level, operational skills and working capacity, and launching various forms of labor competitions To enhance the enthusiasm and creativity of the staff and workers.
Strengthen the reasonable arrangement of operators. The reasonable arrangement of personnel is the most important in the management of the high-grade scarf factory. If the personnel is messy, if the arrangement is not well unified, or if the arrangement is unreasonable, it will lead to the management confusion Also will be very difficult to complete the target task of high-grade scarf manufacturer, so how can ability achieve reasonable arrangement First of all, we must divide the personnel into several levels. Those with high technical culture are one level, those with culture but without technology are one level, those with technology are one level, and those without technical culture are one level. In this way, after we have separated the levels, then the staff according to the post needs to be integrated to each post, such an arrangement will be high-grade scarf manufacturers to bring certain convenience in the overall management of production. Secondly, staff training in the high-grade scarf manufacturers in the management of personnel is an indispensable job. As a director of a high-grade scarf manufacturer must make a detailed training plan, which is a very important job, in the future management will play a very important role, training plan can include, etc. .
Defects and preventive measures in the process of FLUFFING OF WOOLEN CASHMERE SCARF
1. BEVELLED, broken edges
Causes: improper raw material ratio of the edging yarn, resulting in a big difference between the edging yarn and the Cloth Surface, poor edge organization, loose tension of the edging during warping, unironing of the fleeced edge, and long-term wear of the fleecing card clothing, resulting in sharp and blunt in the middle of the card clothing on both sides of the Card Roller Inconsistent fuzzing.
Preventive Measures: 50 Wool / 50 viscose blended yarn is used as edging, and 2 / 2 Henry Fong is used as edging to make edging and fabric felting the same, while warping, the tension of edge brace is adjusted to make edging and fabric tension consistent; Always adjust the position of the fabric on the needle roller when fluffing. Avoid using the middle position so often that the sharpness of the two sides and the middle of the needle cloth is not the same.
2. HAIR MARK
Causes: Uneven fabric tension; too tight rubbing ear, ear root hair marks.
Preventive Measures: adjusting tension at any time in the process of fuzzing to keep the cloth flat; or light steaming before fuzzing to make the cloth flat; rubbing can not be too tight, should meet the technical requirements of the scope.
3. UNEVEN WATER PATTERN
The water mark is the most remarkable appearance characteristic of cashmere scarf. It determines the luster, feel, and appearance of the cashmere scarf. Whether the water ripple is even or not depends on the uniformity of the Bristle of steel wire and the wet brush of prickly fruit.
Preventive Measures: According to the fabric fabric structure to formulate the fuzzing process, adjust cloth speed and tension to coordinate with each other, keep the cloth surface flat, strive to under the premise of small tension to take out even and dense underfleece, lay a good foundation for wet brush: The installation of pricking fruit should be flat, the moisture content of the fabric should be even when wet brushing: Before the wet brush is fixed, the spike should be placed outside the cloth surface to avoid the scar left on the cloth surface when the wet brush is fixed Affect the effect of the cloth surface: fuzzing and wet brush must be in accordance with a positive and negative order, to ensure the positive and negative water texture consistent.
How to use functional finishing of CASHMERE SCARF
After finishing process requires products in the wet and dry shop repeated finishing. In order to prevent the auxiliaries from dissolving and losing in the wet finishing process and ensure the finishing effect, the finishing auxiliaries should be added in the last wet finishing process Therefore, we should also consider to avoid the adverse effects of functional finishing on the physical and chemical finishing processes. Based on the above-mentioned and several experiments, the process route is as follows: Wet finishing-dry finishing-wet finishing-wet brushing roll (two soaking and two rolling) baking-baking-bristle-steaming-finished product.
Under the high temperature condition, not only must guarantee the full cross-linking reaction of the finishing assistant to achieve the anticipated finishing effect, but also must consider the change of the mechanical properties of cashmere fiber under the high temperature condition and different treatment time But affects the product color light and the Intrinsic Quality. Soft water must be used to avoid calcium, magnesium ion and other impurities in hard water deposited on the fabric surface and affect the finishing effect. The cashmere scarf after antistatic finishing has obvious antistatic effect and improves the wearability of the product.
The water and oil repellency of the finished fabrics were improved to meet the standard requirements. All the physical indexes of the finished fabric reached the standard, and the dyeing and rubbing fastness were improved.
Cashmere woven products belong to high-grade clothing fabrics, and there are strict requirements for their use and maintenance. If we can reduce the number of dry cleaning as much as possible, it will play an active role in promoting the use of cashmere products The Market Outlook and benefits will be very positive.
The principle of functional finishing of CASHMERE SCARF
The principle of antistatic finishing is to increase the conductivity of the fabric so that the accumulated static electricity on the surface of the fabric can be discharged in time. At present, the commonly used methods include adding conductive fiber and adding antistatic agent to deal with 2 kinds.
Because antistatic wire only dark gray and light gray 2 kinds and can not be dyed, so the finished scarf color is limited, only with antistatic wire close to the color can be applied. In addition, due to the addition of anti-static wire, the scarf feel has a certain impact. For fuzzing products, the anti-static filament is easy to be broken in the finishing process, so the method of adding additives is adopted to achieve the anti-static effect.
The purpose of functional finishing is to increase the additional functions of antistatic, machine washable, waterproof, oil-proof and stain-proof on the premise of not affecting the permeability and other wearability of the fabric.
The principle of machine washable finishing is to form a reticular membrane on the surface of cashmere fiber by chemical bonding between the active groups in the silicone resin and the active groups in the cashmere fiber protein molecules The directional friction effect caused by the scale structure of cashmere is eliminated and the felting shrinkage is prevented. The treatment technology does not contain fluorinated oxidant and meets the requirement of environmental protection. The processed product can not only meet the machine washable standard, but also increase the anti-pilling property and improve the air permeability.
Anti-finishing is to give the fabric excellent water-repellent, oil-repellent and anti-fouling properties. Through the finishing of three anti-additives, the auxiliaries are oriented on the surface of the fiber, thus forming a polymer film on the surface of the fabric The critical surface tension is reduced so that the fabric can not be wetted with oil. Because the surface tension of water is greater than that of oil, the treated fabric is both water repellent.
MANUFACTURING TECHNOLOGY OF BURNT-OUT CASHMERE
1. Selection of RAW MATERIALS
Burnt-out products require the use of 2 types of fiber materials with different properties, one type is cashmere and silk protein fiber, the other is cellulose fiber. Cashmere and silk soft, smooth, with the matching cellulose fiber should have a similar appearance characteristics, so decided to use velvet and tencel blended. Chemical agents will be part of the tencel rotten, and velvet part is not corroded, made of translucent pattern products.
2. Yarn Design
Tencel yarn is purchased from outside, YARN LINEAR DENSITY is. The strength, yarn density and
yarn evenness are required to meet the Enterprise Standard to ensure the appearance quality and internal physical index of the finished product.
3. Technical Highlights
This product uses the low linear density velvet blended yarn, the yarn strength is relatively low, and the fabric structure is more compact than ordinary worsted cashmere scarf, so the yarn is easy to break when weaving. To reduce the number of severed heads. To improve the production efficiency and the quality of grey cloth, the following measures are taken in the production process: adding warping oil during warping to increase the strength of the yarn and reduce the friction between the yarns, so as to reduce the broken ends in warping and weaving; Reduce Loom speed to reduce weaving broken ends.
4. DESIGN OF WEAVE AND FABRIC STRUCTURE
In order to highlight the pattern of three-dimensional sense, the product adopts double-layer weave. Bottom with velvet blended yarn, plain weave; flower with Tencel Yarn, 2 / 2 twill weave. In order to make the pattern more delicate, contour lines more clear and tidy, surface to interior yarn arrangement than design: Tencel / Velvet 2 / 1.
Dyeing and finishing technology and requirements of burnt-out CASHMERE SCARF
The selection criteria are high solid content and low viscosity, good viscosity and Rheology, good wettability, does not contain any pigment, soluble in water, easy to wash after fixing, has good permeability and wettability, acid and Alkali oxidant resistance. The quality of the product is related to the color rate, shade, reproducibility, pattern clarity and uniformity. We choose White Slushee, synthetic dragon gum and emulsified paste mixture.
The quality of the product is directly affected by the proper preparation of the pulp. Concentrated sulfuric acid is used as the reagent, which has the advantages of low cost and convenient operation. In order to make the pattern lines neat and clear, the bottom tencel part is clean and no residue. After repeated tests, the best formula of the pulp is obtained: Mixing Mixture 600-700 ml / l, concentrated sulfuric acid 30-50 ml / l, water 300-400 ml / l.
Ground color dyes use weak acid dyes, dyeing cashmere part of the color, and tencel part of the color, so as to maintain the whiteness of the fabric surface, the general choice of Sandland and color Pinot dyes.
Reactive dyes are used in printing paste, which can dye tencel partly, have good solubility in low temperature and a little water, and have high dye-uptake, saturated color after steaming for 30 min. Its brightness and color fastness meet the requirements.
Carbonization temperature directly affects product carbonization degree, appearance quality and degree of difficulty in washing. If the temperature is too low, the burnt pulp printing part is opaque white, which is not easy to clean, thus resulting in charring dirty; carbonization temperature is too high, the burnt pulp part is black brown, and its residue sticks to the surface of the ground tissue cashmere fiber, and is not easy to clean And the texture of the surface is also black-brown, a serious impact on the appearance and internal quality of products.
Through steaming to make printing part solid color, so that the dye dyed out saturated color and lustre. When steaming, raising the temperature of steaming box is beneficial to coloring, but the temperature is not easy to be too high to prevent color change. General use of saturated steam, temperature in 100-105 °C, steam humidity, to the amount of color, but not to make the pattern leakage or produce color as a degree. The normal evaporation time is 30 min.
Wash the spun silk part of the product. The temperature of the wash cloth is not easy to be too high to prevent the washed dye from re-dyeing on the fabric, resulting in staining and floating color. At the same time, the temperature is too high to produce felt shrink Therefore, washing
temperature is generally controlled at 25-35 °C for 30 minutes.
The technology of embossing and printing of DRAPE SCARF
1. PROCESS LINE POLYESTER
Nylon cloth a white a rolling wrinkle a transfer printing a cut a finished scarf
Fabric Specification
WARP: 83dtexDTY Polyester Filament (Web)
WEFT: 83dtexDTY Polyester (1000 twist / M)
Meridian density: 200 Root / 10 cm
Weft density: 180 Root / 10 cm
Fabric width: 210 cm
After Rolling Width: 135 cm
STYLE FEATURES
This scarf is characterized by wrinkle when the pattern is complete, stretched out to reveal the background of the original fabric pattern is not complete. Suitable for rough, deep, hard, straight drape, form the style of rough, with a little wild beauty. Patterns can be selected in the natural animal pattern, such as leopard, snake pattern, and so on.
DESIGN ESSENTIALS
(1) pay attention to the conformity of the direction of the wrinkles with the pattern requirements of the finished product. If the scarf is a long scarf, the rolling direction should be suitable to the weft direction, in the use of the process, can show the wrinkle inside the fabric color, so that the scarf in the use of the process appears rich layers, rich changes, fully display the special effect after pulling apart. If the warp direction, then the scarf in use, the fold is fully folded, can not see
the effect of the fold, rolling the fold lost its meaning.
In the transfer printing of fabrics, attention should be paid to the control of dyeing quantity. Too Much, dyeing, fold in the primary color will infiltrate into the dye, destroy the aesthetic; too little, the printing mold, affect the quality. The specific method is to control the printing speed and temperature, so that the contact time between cloth and printing paper can not be too long, so as to avoid too much dye sublimation and infiltration into wrinkles, wrinkles style effect.
Processing Technology of goose down fur scarf made by scarf manufacturer
Clean the raw goose immediately after it is skinned. To scrape the remaining meat and fat from the skin, it can be done by hand or in a sub-oiling machine. Scraping Board from the tail to the head, force to uniform, while scraping edge with a towel, Sawdust and other rubbing board, to prevent oil pollution of the fur. After cleaning should be taken as soon as possible anti-corrosion measures, otherwise the fresh skin is easy to autolysis and deterioration. The anticorrosion may use the natural shade dry method or the salting method.
1. Dry in natural shade
Nail the Leather Board flat on the board, fur down, leather board up, on the ventilation of the cool place dry. As the goose fat melting point is very low, 20 °c-30 °C will be dissolved, such as the spread of goose oil to the skin, will increase the processing difficulties.
2. Salting method
1 Salting. Sprinkle salt evenly on the surface of raw meat. Use 20%-30% of the fresh skin weight. After skimming salt, stack the leather sheet layer by layer against the leather sheet, shake off the salt and dry again after 15 days.
Salt leaching. Soak 25 tea in Salt Water for 24 hours, remove and stack in the same way for 5 days, then open flat to dry. The drying method is the same as the natural drying method.
The temperature should be 10 °C ~ 20 °C and the relative humidity should be 60% ~ 70% . When the moisture content of skin is reduced to 10% ~ 20% after dry in shade, it can be stored in warehouse. Leather should be placed in a well-ventilated place, classified pile, each pile of not more than 30 for Xuan. And spreading insect repellent to be sent to the Tannery for tanning.
Goose down fur can be made into scarf wearing cold insulation, beautiful and generous, favored by consumers, has broad prospects for development.
INK JET PRINTING PRINCIPLE OF SCARF MANUFACTURER
Ink Jet Printing works in much the same way as inkjet printer. By applying an external force to the ink, it is sprayed through a nozzle onto the fabric to form spots of color, which in turn form a pattern. Digital ink-jet printing by digital technology to control the nozzle spray and do not spray, spray out what color of ink. The jet moves in the XY direction to ensure that the desired image and color are formed on the fabric surface.
There are two ways of Digital ink-jet Printing: one is a continuous jet, and the other is on-demand jet.
1) the principle of continuous jet digital printing is that by applying high frequency oscillation pressure to the ink, the ink is ejected from the nozzle to form a uniform and continuous micro-drip flow. An electric field is arranged at the nozzle which changes synchronously with the photoelectric conversion signal of the pattern, and the ejected liquid drops are selectively charged in the charging electric field. When the flow of the liquid drops continues to pass through the deflecting electric field, the charged liquid drops are deflected under the effect of the electric field, and the non-charged liquid drops continue to fly in a straight line. The straight flying liquid drops can not reach the substrate to be printed and are recycled by the collector.
The principle of the on-demand jet printing system is: When printing is needed, the system applies high-frequency mechanical force and electromagnetic thermal shock to the color ink in the nozzle, causing it to form tiny droplets which are ejected from the nozzle Computer-controlled spray to a set pattern. On-demand jet is the most widely used thermal ink-jet technology, it is based on the heat pulsation to produce ink drops, by computer control of a resistance wire heated to the specified temperature, so that printing ink vaporized from the nozzle after the injection.
Production Technology of worsted MERCERIZED ANTIBACTERIAL CASHMERE SCARF
1. Spinning
SPINNING PROCESS OF MERCERIZED WOOL YARN A: Model B412 mixing frame model B423 cross-stitch combing machine model B432 cross-stitch combing machine model B442 open-stitch combing machine model FB44l ring roving machine FB441 ring roving machine SAVIO-m bobbin machine Italian Espero-m Bobbin Machine ICOMATA No. 23 Doubling Machine id90-m Doubling Machine H032 steaming yarn machine.
The roving quality is strictly controlled at 0.2 g / M, and the roving adopts 2 passes. Small draft, the distance should be small, so that the roving reach light, round, tight. The Front Spinning increases the mixing times as much as possible; the drafting multiple of the spun yarn is not easy to be too large or too small; otherwise, the yarn will deteriorate, depending on the length of the fiber, the choice of spacing is not easy to be too large or too small. Select drafting 17 times, spindle speed 5500r / Min.
II. Weaving
The specifications of Grey Fabric, the number of heddle pieces is 4, the heddle-piercing method is flying through 1,3,2,4, the side-thread-piercing method is double flat-piercing method L, l, 3,3, the general requirements for technical parameters such as warping, winding and beating are low tension and high back beam In order to avoid yarn broken end and sparse close-file weaving defects.
3. Finishing
The technological process is as follows: dyeing, washing, antibacterial, soft finishing, dehydration, drying, inspection and packing.
1. SUSPENSION DYEING PROCESS: With suspension dyeing method, HAc3% , yuanmingfen 5% , leveler SET0.5% , bath ratio 1:70, light pink dye is Pula 10B0.004% , youhui is 0.1% , dark blue dye is Joseph Lanner free and easy red G0.04% , Joseph Lanner free and easy red b 0.03% , Joseph Lanner free and easy blue 2R0.14% ; Dyeing Heating Curve.
2. WASH: add pillow oil wash 5% , 20-30 °C wash for 5 minutes, do not need a greater effort to wash.
3. Anti-bacterial soft finish: Chitosan is a new environmental protection material, which is rich in resources, non-toxic, non-pollution, has good Biocompatibility, biodegradability and broad-spectrum anti-bacterial property, and is applied to the anti-bacterial finish of fabrics. The wool treated with Chitosan has antibacterial activity.
Technological Process: The fabric was soaked in the finishing solution containing 0.2% chitosan, 0.6% citric acid and 2% softener for 30 min (room temperature condition) , then double-dipped and double-rolled on the electric mini-mill, the rolling liquid ratio was 70%-80% , then dried for 7 min and baked at 120 °C for 2 Min 40-50 °C hot water full wash, cold wash, and finally drying. The performance of the finished scarf is tested. The results showed that the antibacterial rate of the scarf treated with Chitosan and its derivatives could reach 80% , and the antibacterial rate of the scarf treated with Chitosan and its derivatives could reach more than 50% after 20 times of washing, and the antibacterial rate of the scarf treated with Chitosan and its derivatives could reach 80% and 50% respectively It shows good washing resistance.
Design of worsted mercerized antibacterial CASHMERE SCARF
With the diversification of the market requirements, the development of fashion scarf by more
and more people’s attention. The worsted scarf of mercerized wool, with the characteristics of being not easy to felting, not easy to pile up and so on, can meet the different needs of the majority of consumers for scarf products, and has the characteristics of comfortable use, strong three-dimensional feeling and good decorative effect At the same time, it is a kind of textile with high added value.
Raw Material Selection and yarn design: mercerized wool is used as raw material, the average fineness is 17.5 Um, the Coefficient of dispersion of fineness is 2.78% , the weighted average length is 76.02 mm, the Coefficient of dispersion of length is 34.11% . Yarn A is 16.7 Tex 2 mercerized wool with a twist factor of 85140, and Yarn B is 2.7 Tex Lycra, a stretch fiber developed by the DuPont.
Fabric Weave: many times of trial and error have been done in the selection of fabric weave structure. As the LYCRA yarn is used in this product, the yarn has certain elasticity, so it is difficult to weave on the machine, and its tension is not easy to grasp Warping is more difficult. After repeated contrast test, the product is confirmed to be plain weave.
Specification design: The designed product specification is: Strip length 387 cm, width 150 cm, warp density 106,10 cm, weft density 106,10 cm, mass 105 G / M.
The use of mercerized wool, so that the product is not easy to felting, not pilling, soft feel characteristics. A certain number of Laika yarns are arranged at regular intervals between the warp and weft direction. Under natural conditions, due to the shrinkage of the elastic yarns, the uneven surface of the fabric forms a bubble shape, and the four edges are shaped like wooden ears. They have a strong three-dimensional sense and have a relaxed and fashionable style Give a person with brand-new feeling, get people’s affection quite. Through anti-bacterial finishing, the product has more anti-bacterial functions, meets the higher requirements of consumers, uses the hanging dyeing process, so that the product has the characteristics of gradual change in color.
Two typical methods of making pleated scarf
Some scarf fabrics are very light and thin, but also to reflect the effect of Bar, Bar, Bar Pattern is difficult to print in the printing machine, and very light fabric in the ginning machine and easily damaged. In production practice, the yarn-dyed fabric with hand creasing method is adopted.
First yarn-dyed and then wrinkled scarf
1 Technological Route
Polyester dyed yarn a weaving, fabric a cut a sewing edge a hand folded into a bundle with a rope tied tightly a steamer box finished
2 Fabric Specifications
WARP: 56dtexFDY polyester yarn (800 twist / M)
WEFT: 56dtexFDY polyester yarn (800 twist / M)
Meridian density: 300 Root / 10 cm
WEFT DENSITY: 300 Root / 10 cm
Width: 100 cm
CRINKLE BACK DOOR WIDTH: 60 cm
3 DESIGN ESSENTIALS
In the design of Bar, grid, should avoid too fine, too dense, too small bar, grid lines, so that the finished product both rich wrinkles, and fully reflect the Bar, grid effect.
Key points of process technology
(1) the wrinkles are not as firm as those made by machines. Therefore, it should be noted on the washing mark that high-temperature ironing is not allowed.
(2) the effect of creasing should be folded according to the design, and the creases of each scarf are slightly different, which makes it more colorful.
(3) the temperature and time of steaming box should be determined according to the design requirements of fabric thickness and pattern wrinkle, and samples should be made first, parameters should be determined and then put into production.
Second, the use of SPANDEX WEAVING SHAWL WRINKLES
1 Technological Route
Polyester Yarn Warp + Polyester Yarn Weft + spandex-weaving-training cloth-scouring and bleaching-handwork bench printing-rinsing and natural shrinkage-cutting-finished scarf
WARP: 83dtexDTY Yarn (1500 twist / M)
WEFT: 83 dtexdty Yarn (2000 twist / M) + 33 DTEX
Warp density: 180 / 10 cm. weft density: 180 / 10
Fabric Width: 160 cm
3 STYLE TRAITS
Because this fold is formed by the natural contraction of several SPANDEX threads woven in the middle of the weft threads, its folds appear to be particularly neat and regular, emitting elegant, elegant and well-ordered Rhythmic Beauty This kind of scarf is more suitable with the rich feminine flavor clothing matches.
4 DESIGN ESSENTIALS
(1) because the formation of this wrinkle is dependent on the weft yarn, therefore, the tension is small, suitable for use in light, thin fabric, the formation of fine, dense regular wrinkles.
(2) the use of manual table printing, so in the design of patterns, color can not be too complex, so as not to increase the difficulty of the process, generally within 5 color is more ideal.
(3) the key point of the design should be the design of the SPANDEX yarn in the weft yarn. The length, the length, the spacing and the density of the SPANDEX yarn have a great influence on the final effect.
Quality control of WOOLEN CASHMERE SCARF PRODUCTS
In order to strengthen the quality control of each process in the production process, do not let the problem product flow down the next process, we have strengthened the inspection in the production process. The grey fabric in the weaving workshop is first inspected, followed by a rubbing test after rubbing, then a wet test after washing and shrinking, a middle test after drying, and a finished product inspection. The tests are as follows:
(1) grey fabric inspection includes specification inspection and appearance defect inspection. The specification inspection includes the length, width, spike length and single weight of each scarf; The appearance defects include the spinning defects such as slub yarn and big-belly yarn, and the weaving defects such as skips, taps, nip damage and wrong pattern. The whole piece is then graded and graded.
(2) the thickness and tightness of each ear are checked by rubbing test, and whether it affects the flatness of the cloth surface. Those who do not conform to the standard must be repaired.
(3) wet test specification: length and width of each scarf: appearance defects: creases, curling edges, holes, dirt, etc. .
(4) inspection specifications after drying: Length, width, weight; appearance defects: Broken, broken edge, streak, whether the cloth surface is askew, etc. .
(5) the quality of the finished product: Suede, handle, water grain, Physical Index: the length, width, weight and ear length of each scarf; Appearance Defects: Bevel, Fluff Mark, crack, broken ear, non-conforming to specifications, sparse file, color flower, selling color, dirt and so on.
The internal quality inspection products into the finished product shop before checking with the standard sample, mainly look at the style, feel, specifications; check the process of each process and process card records, in order to have quality problems to implement.
TRADE FRICTION AND CHARACTERISTICS OF CHINESE TEXTILE SCARF PRODUCTS
At the same time that China’s export of textile and scarf products has increased considerably, taking into account the impact on the old system of world textile trade, the export competitiveness of the relatively vulnerable textile industry of some developing countries and the carrying capacity of the European and American textile and garment industry, which has been protected by quotas for a long time, we have adopted a series of self-regulation policies, and made enough efforts, even made sacrifices, to create a new pattern and integration of world textile trade under the new situation.
Compared with the textile trade disputes in the pre-quota period, the trade frictions in the new period have taken on new characteristics, mainly as follows:
1. Trade frictions take more diverse forms and involve a wider range of products. Anti-dumping and technical barriers to trade are still prevailing, and the “Special Safeguard Clause” , which is simple to start and flexible to apply, is increasingly used to restrict the import of Chinese textiles. In March 2007, the European Union (EU) initiated an anti-dumping investigation against China’s eight categories of textiles; in June, the US initiated an anti-dumping investigation against China’s polyester staple fiber involving an amount of nearly us $100 million; and in July, the United States Department of Commerce initiated anti-dumping and countervailing investigations against products such as thin-walled rectangular steel tubes and composite woven bags originating in China, and classified the composite woven bags as textiles (which are not classified as textiles under the customs classification) .
2. Trade friction began to transform from the micro-level to the macro-level. Some media and politicians in some Western countries use trade friction as a pretext, implicating “non-market economy clauses” and Chinese product safety and exchange rate issues, and spreading the “economic threat theory” An attempt to inject unease into China’s foreign relations.
Trade friction is accompanied by trade competition with developing countries, involving more complex stakeholders. In order to reduce the pressure after the quota abolition, the EU and other countries conducted regional trade arrangements, through discriminatory tariffs and detailed “anti-dumping” policy to reduce external competition. Such regional arrangements are increasingly valued by developed countries. Some developing countries or more developed countries in the new regional pattern, the layout of the textile industry, recapture the market. Pakistan, India, Vietnam, Cambodia and other countries labor costs are extremely cost advantage, has absorbed a large number of China’s transfer of European and American textile orders. The competitive environment of China’s textile industry has become more complex.
Design specification of Cashmere light-weight and light-fuzzing JACQUARD SCARF
Cashmere light-weight fuzzing jacquard scarf is suitable for autumn and winter. It has not only good thermal performance, but also a refreshing appearance. We have broken the previous design method of light woolen scarf, in order to fully reflect its light and thin, with a strong three-dimensional characteristics, the use of fine warp and coarse weft yarn configuration, in addition, while ensuring its good appearance characteristics, we also have to consider its inherent quality and cost. To this end, the choice of raw materials and fabric structure design and finishing process must be fully integrated into consideration.
In order to reduce the cost, 120 / 2 Velvet blended yarn is used for warp and 15 / 1 Woolen pure cashmere yarn is used for filling. Under the condition of definite spinning count, the choice of yarn twist Coefficient directly affects the handle, color and processing property of the fabric. In addition, the selection of yarn twist factor must be considered in combination with the yarn
properties, blending ratio and other factors.
Scarf products require soft texture, so the tightness should not be too big, also can not be too small, if the tightness is too small, scarf will appear loose, its strength, tensile performance and other internal quality will be affected. The choice of tightness is critical. Combined with the previous production practice and the design features of this product, we determine the machine warp tightness is 35% , machine weft tightness is 42% . Taking into account the fine appearance of the product, the structure of soft and not rotten, fabric structure using 1 / 3 twill and 3 / 1 twill constitute the jacquard fabric.
Development conception of Jacquard Leno top GRADE SCARF
Leno fabric has a long history. Due to its complex process and low production efficiency, modern Leno fabric has gradually dropped out of the market. However, in recent years, people’s pursuit of novelty and novelty in the textile industry has gradually brought Leno fabric back to the fore And applied to many new areas. Leno Fabric has unique texture effect, product quality light, transparent, thin, especially in line with the elegant, light, elegant silk products, suitable for the development of high-grade personalized silk products.
1. DESIGN INTENT
Using Mulberry Silk As warp and thick mulberry silk as Weft, the fabric with fine texture and obvious pattern is produced and used to make high-grade scarf.
2. Conceives
The floral pattern is composed of plain, varied and other tissues. Using the complex Leno tissue as the ground part, the ground part can form the texture effect that the grains are interlaced, and the middle part of the flower part is filled with plain tissue, which makes the flower part of the product appear dense and form a contrast with the ground part The flower margin is delineated by a variable texture. The length of the weft fills the outline of the flower pattern; the interspace of the flower pattern is formed by a strand of tissue.
The Leno products have higher requirements for yarns and need to be optimized, requiring the warp to meet the requirements of straightness, good winding property, easy twisting during weaving, no slippage of the WEFT, and the formation of clear and uniform-sized holes on the cloth surface Therefore, the General Twist Mulberry Silk is chosen as the warp. At the same time, in order to make the textural effect of the Leno Tissue Outstanding, the thick mulberry silk is used to interweave the WEFT.
PRODUCTION TECHNOLOGY OF CASHMERE BLENDED SCARF
Most of the orders are for 315G / M products, and 62.5 tex yarn is the main yarn for scarf and Shawl. From the angle of production and product quality, 62.5 tex single yarn is used for warp and weft of woolen blended scarf. Twist Selection 560 twist / mPz twist. According to the finished product weight requirements and the most favorable weaving density, choose warp, weft raw material ratio.
The choice of texture is related to the mechanical properties of the fabric, as well as the appearance and handle of the fabric, as well as the consolidation fastness and weft density of the wool. The fuzzing of the fabric mainly depends on the fuzzing of the weft yarn, and the fabric with longer weft floating yarn has better fuzzing effect.
Japanese Kyowa wool machine was used to make white cashmere and fine wool (without dyeing) . According to the characteristics of the equipment and the conditions of the workshop, the moisture regain of the machine is controlled at 26%-28% , the oil content of the machine is controlled at 2.5%-3.5% , and 1% antistatic agent is added into the crude oil.
Carding is an important process in the spinning process of woolen yarn. The quality of roving directly affects the quality of the finished yarn.
KNEAD the ear of raw scarf with hands for 1.2 min before shrinking to make the ear fully felted to
prevent the finished ear from untwisting and dispersing. In order to reduce the damage, do not damage feel, cashmere fabric using neutral shrink. Keep the PH around 7.5. The roll pressure is 300 KPA. Shrink cloth temperature control to 32-35 °C.
Rinsing is mainly to use water to wash away the shrinkage agent added, so that the cloth surface is clean, convenient for finishing the next process. It is usually about 30 °c warm water, 5-10 Min.
Steam Brush should be noted: 1 for the poor strength of the scarf must be reduced contact point, reduce cloth speed and brush roller speed, otherwise easy to tear scarf. 2 speed, give steam to be uniform, otherwise brush hair effect is not uniform, before driving to exclude condensation water, otherwise easy to form rust spots. 3 brush hair must pay attention to the hair on the cloth, and brush roll to the same direction, otherwise prone to hair to disorder. When brushing fabrics of different colors and Lustre, must clean the brush roller to prevent staining.
Steaming can not only play a good shape, but also can make the fabric surface smooth, produce a natural soft and lasting luster, also can improve the feel, make it more elastic.
The key process of cashmere blended cashmere scarf is felting, fluffing, brushing, shearing and steaming. The research and application of the processing technology of cashmere blended cashmere scarf products are not fixed, the reasonable collocation of raw materials and optimization of processing conditions can make the product design and production meet customer needs.
HOW TO DESIGN HIGH-GRADE JACQUARD GAUZE SCARF
1 / Texture Design
1. Basic Organization: The Leno Organization, a Skein of one organization, plain, change
organization, the Edge Organization is 2 / 2 through the heavy flat organization. The structure is as follows: Complex lenticular tissue, tissue circulation RJ = 24, R W = 4. The motion law of the WARP is different. In the first group, there are 12 warp, 6 warp and 6 WARP, WARP: WARP = 1∶1. After the WEFT is woven into 3 plain weave, the warp and warp twist each other once. In Group 2,12 warp threads were still 6 and 6 ground warp, and the ratio of ground warp to ground warp was 1∶1. After the WEFT was woven into 1 plain weave, the ground warp and the ground warp twisted each other once, and then 2 plain weave were woven.
Floral Part 1: Plain weave. Flower Part 2: Changing structure, used for edge covering of pattern edge, 1 / 2 right twill for Ground Warp and full-lift for stranding warp. Flower 3: A skein a tissue, that is 1 skein group has 1 skein and 1 ground warp, each weaves 1 weft, skein and ground warp twist each other 1 time.
2. Pattern requirements: Pattern design for a single flower, in order to fully express the texture of the local Leno Organization, select the clear ground pattern. The Flower Department chooses the auspicious traditional patterns such as Phoenix and Peony, and makes the flower pattern in turn in the middle of the scarf. The upper and lower edges of the scarf adopt the succinct block-shaped Peony Flower Pattern. The whole is steady and graceful, elegant and Noble, with Oriental Artistic Beauty.
3. CHECK EDGE: Horizontal, double needle check edge at the intersection of Leno and Leno; vertical, Leno for the ground, separated by 3 weft holes, need to meet 3 integral times transition check edge; red and green, plain ground pick-up, double Leno Check Edge; blue and green, in order to make the shed back to the open shed, the yarn hole pattern outer edge is flat, double hook is suitable.
4. Rib Plate Rolling method: According to the method sheet, the rib plate is often made in front of the Leno section with full holes, and the RIB plate is easy to be damaged Namely every 16 needles practical 8 needles, in order to extend the service life of the pattern plate.
2 PROCESS DESIGN
The technical specifications of the products are as follows.
Warp combination: (22.2 / 24.4 DTEX 1 Mulberry Silk 800 twist / M Z 2)680 twist / m s; Weft combination 44.4 / 48.8 dtex 4 Mulberry Silk 180 Twist / M S; Reed Number 12 feather / cm; Reed Number 2 penetration, the Reed has an internal width of 88 cm, a side width of 1 cm 2, an internal width of 58 cm and an external width of 60 cm, and a density of 240150 / 10 cm The number of filaments is 2112 + (side)482 = 2208. Side Warp Piercing method: The straight side is 2 / Harness, 2 / Harness / Reed, Altogether 11 reeds, total 442, small side is 4 / Harness, 1 / Harness / Reed, Piercing 1, Count 4 Reeds 2. The assembly is made by double single hanging, single flower, and the weaving shrinkage is 8.52% .
HOW DOES THE FOREIGN TRADE SCARF FACTORY MOLD THE MARKET COMPETITIVE POWER
1. Set up the strategic consciousness of making use of the Internet to mold the market competitive power foreign trade scarf factory set up the strategic plan consciousness, form the scientific management idea. The practice shows that the management concept and Development Direction of foreign trade scarf factory depend on the strategic and forward-looking development plan of foreign trade scarf factory to a great extent. Many foreign trade scarf factory management decision-makers pay little attention to this, often relying on their own intuition and experience, on the direction of foreign trade scarf factory development, management and decision-making, etc. Due to the lack of scientific qualitative and quantitative analysis and research, it is difficult to make the survival and development of foreign trade scarf factory problems. The Internet has become an indispensable part of people’s life. In the face of such a huge market, foreign trade scarf factory only with the help of the Internet to shape market competitiveness, to objectively face the changing market environment, better survival and development.
2. Pay attention to the construction and management of the network brand in the market economy with increasingly fierce competition, the consumer’s choice of goods is becoming more and more diversified and rational, and the motive of the purchase decision is brand to a great extent. Brand is a product or even a foreign trade scarf factory different from other products and foreign trade scarf factory logo, is to shape the market competitiveness of foreign trade scarf factory a sword. But our country foreign trade scarf factory does not pay attention to the brand accumulation, also does not pay attention to the brand idea extraction and the management. In the Internet Age, consumers are more likely to learn brand knowledge from the Internet This includes the brand profile, the brand history, the story of the brand spokesperson, product features, promotional information, and other user reviews of the brand on the web. Therefore, foreign trade scarf factories should pay attention to the construction and operation of network brands, use network advertising to enhance brand awareness, use foreign trade scarf factory websites to effectively cultivate brand reputation, and use network public relations to effectively maintain brand personality It is hoped that the brand of foreign trade scarf factory will leave a deep and lasting impression on the consumers, so as to seize the market and improve the market competitiveness of foreign trade scarf factory.
In short, in the Internet environment, foreign trade scarf factory to their own market competitiveness and the new characteristics of the market, the full use of the Internet to shape their own market competitiveness, long-term survival and development.
Defects in the key process of WOOLEN SCARF AND ITS PREVENTION
1. Defects in coiling process and preventive measures (1) causes of uneven thickness of ears: the number of warp yarns per ear is not the same. Preventive Measures: strictly in accordance with the technical requirements of the number of twist. The edge yarn is twisted separately, and the dividing line is thrown out. Sequence Control (2) the cause of the different tightness of the panicle: The number of twists per panicle was different. Preventive Measures: The number of twists per spike should meet the technical requirements, that is, (402) twist / root, too loose spikes are easy to be broken in the process of shrinking, too tight spikes are easy to produce hair marks in the roots of spikes when they are fluffing, and the tightness of upper and lower spikes of each frame should be the same The dividing line goes through the middle.
Defects in shrinking process and preventive measures (1) reasons for non-conformity of shrinking specifications to process requirements: Improper operation, non-strict Implementation of process standards; unreasonable process design, resulting in too long or too short shrinking time. Preventive Measures: to strengthen the trial production of pioneer products, to revise the shrinkage coefficient and the width and length after shrinking according to the finished product specifications made by pioneer, to strive for the quality and weight of the products; to strengthen the responsibility of the operators, requirements in shrinking the process of many downtime measurement specifications. Whether the length and width of the shrunk product can meet the technological requirements is strictly checked through the wet check. In general, the length tolerance of a single scarf should be 3 cm, and the width tolerance should be 2 em. (2) causes of breakage, breakage and creasing: too fast running speed or too small retracting; too much pressure or insufficient retracting dose on the retracting drum; too low temperature of retracting wool; too long retracting wool. As the scarf fabric shrinkage can not be cylinder, shrink time is too long it is easy to appear Bar creases. Preventive Measures: Speed should not be too fast. The necking should be less than 120 m / min from big to small, should not be less than 8 em, the drum pressure should be suitable; necking material should be uniformly fed, the speed of the car should be less than 60 m / min; the temperature of necking material should not exceed (45 + 2) °C strictly controlled Shrink time is usually about 1.5 hours.
Development and production process of WOOL PRINTED SCARF
The wool printed scarf is popular with women because it not only has beautiful and amazing outsourcing, but also feel and texture is very comfortable.
Check out some of these tips from Sageoda below.
The production process of digital printing has got rid of the traditional process of color separation and sketch, film making and screen making in the production process, so that the original process line is greatly shortened, the single speed is fast, the cost of proofing is reduced, and thus the production time is shortened. The shortening of proofing cycle and the reduction of cost bring more market opportunities to enterprises. Digital Printing is environmentally friendly, does not damage the fabric feel, good permeability, beautiful pattern, clear layers, especially the transition color (gradient) fine patterns of printing, Color Fastness 4 above the advantages of other printing technology is unmatched. Wool worsted scarf is a high-grade consumer goods, its personalized requirements are strong, so the use of digital printing technology printing, both in line with the wool personalized requirements, but also in line with the wool small batch, multi-color requirements. Digital printed wool scarf pattern clear, soft color, soft feel, in line with the design requirements.
Process flow: Spinning, weaving, mending, washing, drying, steaming, printing, fleecing, softening, drying, steaming, disassembling, knitting. Tie it off.
Printing process: Sizing a drying a printing a Yin, drying a steaming a washing a drying. SIZING: to make the fiber and dye combine quickly and evenly, the scarf is starched before printing. Sizing is a key process before printing, which directly affects the printing quality. Sizing also helps to flatten the cloth surface and keep the same size. Dry in the shade and dry: The printed scarf should be placed for 7-8 hours to allow it to penetrate naturally into the shade to prevent the dye from floating on the surface of the fiber. After drying in the shade, put it into the oven and bake it at the temperature of 50-60 °C for 2-3 hours to make the scarf completely dry. Make sure the drying temperature is not too high. Steaming: the Dye is diffused into the fiber and fixed on the fiber by steaming 20-30rain at 100 °C in the steamer. In the process of evaporation, water droplets caused by local cooling should be avoided. The scarf should be separated by cloth to avoid staining. Rinse: The purpose is to remove the float and fix the color. Wash the dye and dye, residual dyes and chemicals from the scarf with water. Add 2%-3% anti-staining agent (OWF) to cold water, and wash 5-10rain into the scarf. Rinse with plenty of water 2-3 times dehydration, drying.
DESIGN METHOD OF HIGH-GRADE SCARF
The Textile History of 5,000 years has left many valuable traditional weaving techniques for people, how to use them rationally, expand the ideas of product design and development, innovate the design of traditional fabrics, and enrich the textile processing technology, increase the added value of textile products and so have great practical value, product designers should continue to explore and carry forward.
In order to fully express the effect of the texture of the Leno tissue of the ground part, the clear ground pattern is selected. The Flower Department chooses the auspicious traditional patterns such as Phoenix and Peony, and makes the flower pattern in turn in the middle of the scarf. The upper and lower edges of the scarf adopt the succinct block-shaped Peony Flower Pattern. The whole is steady and graceful, elegant and Noble, with Oriental Artistic Beauty.
2 Rib Plate Rolling Method it is known from the rolling method specification that the rib plate is often made in the section with full holes in the Leno weave part, and the RIB plate is easy to be damaged Namely every 16 needles practical 8 needles, in order to extend the service life of the pattern plate.
3 OTHERS
3.1 technological process warp: Raw Material → impregnation → winding → twisting → doubling → twisting → setting → reversing → warping → weaving WEFT: Material → impregnation → winding → doubling → natural setting → reversing → weaving.
3.2 when making a scarf, two pieces of fabrics of different colors are sewed together to form a scarf, which increases the thickness of the object. At the same time, as the upper and lower layers of the fabric are very thin and transparent, the colors of each other can be interlaced through the Yarn Holes Increase the product color space mixing effect.
FABRIC DYEING PROCESS
1. Practice Bleaching
Natural fibers contain impurities, and in the process of textile processing, various size, oil and contaminants are added. The presence of these impurities not only impedes the smooth dyeing and finishing process, but also affects the wearing properties of fabrics. The purpose of scouring and bleaching is to remove the impurities from the fabric by chemical and physical mechanical action, make the fabric white, soft and have good permeability, so as to meet the requirements of wearing, and provide qualified semi-finished products for dyeing, Printing and finishing.
The main processes of scouring and bleaching of cotton fabric are: Preparation of raw cloth, singeing, desizing, scouring, bleaching and mercerizing.
The preparation of the original cloth includes the inspection of the original cloth, the rewinding (batching, sorting, printing) and the sewing head. The purpose of raw fabric inspection is to check the quality of grey fabric and solve the problems in time. The content of inspection includes two items: Physical Index and appearance defect. The former includes the length, amplitude, weight of the original cloth, warp and weft yarn density and density, strength, etc. . Usually spot-check the total amount of about 10% . After the original cloth is inspected, the original cloth must be batched and divided into boxes, and printed on the head of the cloth, indicating the variety, processing technology, batch number, box number, release date and the code of the cloth Turner, so as to facilitate management. In order to ensure continuous batch processing, the original cloth must be seamed.
2) SINGEING:
The purpose of singeing is to burn off the fuzz on the cloth surface, to make the cloth surface smooth and beautiful, and to prevent uneven dyeing and printing defects caused by the fuzz during dyeing and printing. Fabric singeing is a process in which the fabric flat is quickly passed
through a high temperature flame or brushed against a red-hot metal surface. The fluff on the cloth surface heats up quickly and burns, while the cloth body is compact and the temperature rises slowly before it reaches the ignition point That has left the flame or red-hot metal surface, so as to achieve the purpose of burning off the Fuzz, and do not operate the fabric.
4) Boil:
Cotton fiber growth, there are natural impurities (Pectin, waxy material, nitrogen-containing material) together with the companion. After SCARF.COM the cotton fabric, most of the size and some of the natural impurities have been removed, but a small amount of size and most of the natural impurities still remain on the fabric. The presence of these impurities, so that the cotton-weaving cloth surface yellow, poor permeability. At the same time, the appearance quality of cotton cloth is greatly affected by the existence of cotton seed Shell. Therefore, it is necessary to wash the fabric in high-temperature concentrated lye for a long time in order to remove impurities. Scouring is the use of caustic soda and other scouring AIDS and Pectin, wax, nitrogen substances, cottonseed husk chemical degradation reaction or emulsification, expansion, etc..
5) Bleach:
Cotton fabric after scouring, due to the existence of natural pigments on the fiber, its appearance
is not clean enough, used for dyeing or printing, will affect the brightness of the color. The goal of bleaching is to remove the pigment and give the fabric the necessary and stable whiteness without significant damage to the fiber itself. Common bleaching methods for cotton fabrics are sodium hypochlorite, hydrogen peroxide, and sodium chlorite.
The PH value of sodium hypochlorite bleaching solution is about 10, carried out at room temperature, simple equipment, easy operation, low cost, but on the fabric strength damage, low whiteness.
Hydrogen Peroxide Bleaching Solution Ph value of 10, in high temperature bleaching, bleaching fabric whiteness high and stable, feel good, but also to remove the slurry and natural impurities. The disadvantage is that the equipment requirements are high, high cost. In appropriate conditions, combined with caustic soda, desizing, scouring and bleaching can be completed at one time.
The PH value of sodium chlorite bleaching solution is 4 ~ 4.5, carried out at high temperature, which has the advantages of good whiteness and less damage to fibers, but it is easy to produce toxic gas, pollute the environment and corrode equipment, which needs special metal materials to be made Therefore, it is limited in application.
Sodium hypochlorite and sodium chlorite are dechlorinated after bleaching to prevent damage to the fabric due to residual chlorine during storage.
6) MERCERIZATION:
Mercerization refers to the cotton fabric at room temperature or low temperature, in warp and weft direction are under tension, with concentrated caustic soda solution to improve the processing of fabric properties. After mercerization of cotton fabric, due to the expansion of fiber, fiber vertical natural torsion disappeared, cross-section into an oval, the opposite of light more regular, thus enhancing the luster. The increase of the immaterial fixing area of the fiber increases the dye-uptake. The higher the orientation degree, the stronger the fabric, and the setting effect at the same time. After mercerization, be sure to use the wash absorb to alkali or steam box to Alkali, or flat wash to Alkali and other methods to fully Alkali, until the fabric is neutral.
2. , Dyeing:
Dyeing is a process in which a dye is physically or chemically combined with the fiber, or a pigment is chemically produced on the fiber to give the fabric a certain color. Dyeing is carried out under certain conditions such as temperature, time, PH value and dyeing auxiliaries. Dyed products should have uniform color and luster, but also need to have good color fastness. The dyeing methods of fabrics are mainly divided into dip dyeing and tie-dyeing. Dip-dyeing is the process of dipping a fabric in a dye solution so that the dye gradually picks up the fabric. It is suitable for small batch and multi-variety dyeing. Rope dyeing and CRIMP dyeing belong to this category. Tie-dyeing is a dyeing process in which the fabric is first dipped into the dye solution, then the dye solution is rolled into the fabric through rollers and treated with steam or hot melt. It is suitable for dyeing large quantities of fabrics.
What is the craft and application of burnt-out Flowers
The dying process is a printing process in which corrosive chemicals (such as sulfuric acid and ALCL3) are printed on the surface of fabrics made up of two or more fibers. Commonly used in velvet fabrics. The pattern or concave-convex orderly, or translucent, highly decorative. It is also possible to add a suitable tolerant dye in the printing paste, rot one fiber component while another component of fiber coloring, obtain the effect of color rot flower.
Rotten printing was originally used for real silk and its interwoven fabrics, such as rotten-flowered silk, cashmere and Velvet, and later for rotten-flowered polyester / cotton and other fabrics. Burnt-out fabrics are made of two different fibers interwoven or blended, one of which can be damaged by a chemical agent, while the other is unaffected, forming a special style of burnt-out printed fabric.
Fabrics are usually woven or blended from acid-resistant fibers such as silk, nylon, polyester, and cellulose fibers such as viscose, cotton, etc. . The fabrics are dyed with a strong acid substance to blend and printed. After drying, the cellulose is hydrolyzed and carbonized by strong acid After being washed by water, the pattern with translucent visual sense and concave-convex is obtained. With the return of popularity, burnt-out design is often used in a large number of curtains, bedspreads, tablecloths and other decorative fabrics and clothing fabrics.
GENERAL KNOWLEDGE OF GARMENT FABRIC
In the world of clothing, the fabric of clothing is ever-changing and changing with each passing day. Generally speaking, the fabric with comfortable wear, sweat permeability, drape, Visual Noble, soft touch, and other characteristics is high-grade fabric.
Social occasions wear clothing, should choose pure cotton, pure wool, pure silk, pure hemp products. With these four kinds of pure natural texture fabrics made of clothing, most of the higher grade. Sometimes it is permissible to wear clothing made of pure leather.
Below, the characteristics of common clothing fabrics are made a few brief introductions.
1. Cotton
Cotton cloth is a general term for all kinds of cotton textiles. It is used for fashion, casual wear, underwear, and shirts. Its advantages are easy to keep warm, soft close-fitting, hygroscopicity, breathability is very good. Its disadvantage is easy to shrink, easy to wrinkle, appearance is not very clear aesthetic when wearing must often iron.
2. Linen
Linen is a fabric made from hemp, flax, Ramie, jute, sisal, banana hemp, and other hemp fiber plants. Generally used to make casual wear, work clothes, but also more than its production of ordinary summer. It has the advantages of extremely high strength, hygroscopicity, heat conduction, and excellent air permeability. Its disadvantage is that it is not comfortable to wear, the appearance is rough, blunt.
3. Silk
Silk is a general term for all kinds of silk fabrics made from silk. Like cotton, it comes in many varieties and has different personalities. It can be used to make all kinds of clothing, especially suitable for women’s clothing. Its advantages are thin, fit, soft, smooth, breathable, colorful, rich luster, noble and elegant, comfortable to wear. Its shortage is easy to produce wrinkles, easy to suck body, not strong enough, fade faster.
4. Worsted
Wool, also known as wool, it is all kinds of wool, cashmere woven into the fabric of the general term. It is usually suitable for making formal, high-grade clothes such as dress, suit, coat, etc. . Its advantages are anti-wrinkle wear-resistant, feel soft, elegant upright, full of flexibility, thermal strong. Its disadvantage is mainly washing more difficult, not suitable for making summer clothes.
5. Leather
Leather is a fabric made of tanned animal skins. It is used to make fashion, winter clothing. Can Be divided into two categories: one is leather, that is, after the processing of leather wool. The other is Fur, that is, treated with leather with fur. It has the advantages of lightness, warmth and luxury. Its shortcoming is the price is expensive, the storage, the nursing aspect request is high, therefore not suitable popularizes.
6. SYNTHETIC FIBER
Chemical Fiber, is short for chemical fiber. It’s a textile made from macromolecule fibers. It is usually divided into artificial fiber and synthetic fiber two categories. Their common advantages are bright colors, soft texture, drape upright, smoothness and comfortable. Their disadvantages are wear resistance, heat resistance, hygroscopicity, permeability is poor, heat easily deformed, prone to static electricity. Although it can be used to make all kinds of clothing, the overall grade is not high, difficult to the elegant hall.
7. Blend
Blending is the mixture of natural fiber and chemical fiber according to a certain proportion of textile fabrics, which can be used to make a variety of clothing. It has the advantage of both absorbing the advantages of cotton, hemp, silk, wool, and man-made fibers, while avoiding their disadvantages as far as possible, and is relatively cheap in value, so it is very popular. Make in the formal social occasions wear clothing, should choose pure cotton, pure wool, pure silk, pure hemp products. With these four kinds of pure natural texture fabrics made of clothing, most of the higher grade. Sometimes it is permissible to wear clothing made of pure leather.
Below, the characteristics of common clothing fabrics are made a few brief introductions.
1. Cotton
Cotton cloth is a general term for all kinds of cotton textiles. It is used for fashion, casual wear, underwear, and shirts. Its advantages are easy to keep warm, soft close-fitting, hygroscopicity, breathability is very good. Its disadvantage is easy to shrink, easy to wrinkle, appearance is not very clear aesthetic when wearing must often iron.
2. Linen
Linen is a fabric made from hemp, flax, Ramie, jute, sisal, banana hemp, and other hemp fiber plants. Generally used to make casual wear, work clothes, but also more than its production of ordinary summer. It has the advantages of extremely high strength, hygroscopicity, heat conduction and excellent air permeability. Its disadvantage is that it is not comfortable to wear, the appearance is rough, blunt.
3. Silk
Silk is a general term for all kinds of silk fabrics made from silk. Like cotton, it comes in many varieties and has different personalities. It can be used to make all kinds of clothing, especially suitable for women’s clothing. Its advantages are thin, fit, soft, smooth, breathable, colorful, rich luster, noble and elegant, comfortable to wear. Its shortage is easy to produce wrinkles, easy to suck body, not strong enough, fade faster.
4. Worsted
Wool, also known as wool, it is all kinds of wool, cashmere woven into the fabric of the general term. It is usually suitable for making formal, high-grade clothes such as dress, suit, coat, etc. . Its advantages are anti-wrinkle wear-resistant, feel soft, elegant upright, full of flexibility, thermal strong. Its disadvantage is mainly washing more difficult, not suitable for making summer clothes.
5. Leather
Leather is a fabric made of tanned animal skins. It is used to make fashion, winter clothing. Can Be divided into two categories: one is leather, that is, after the processing of leather wool. The other is Fur, that is, treated with leather with fur. It has the advantages of lightness, warmth and luxury. Its shortcoming is the price is expensive, the storage, the nursing aspect request is high, therefore not suitable popularizes.
6. SYNTHETIC FIBER
Chemical Fiber, is short for chemical fiber. It’s a textile made from macromolecule fibers. It is usually divided into artificial fiber and synthetic fiber two categories. Their common advantages are bright colors, soft texture, drape upright, smooth and comfortable. Their disadvantages are wear resistance, heat resistance, hygroscopicity, permeability is poor, heat easily deformed, prone to static electricity. Although it can be used to make all kinds of clothing, but the overall grade is not high, difficult to elegant hall.
7. Blend
Blending is the mixture of natural fiber and chemical fiber according to a certain proportion of textile fabrics, can be used to make a variety of clothing. It has the advantage of both absorbing the advantages of cotton, hemp, silk, wool and man-made fibers, while avoiding their disadvantages as far as possible, and is relatively cheap in value, so it is very popular.
WHAT IS ELECTRIC SPINNING? CLASSIFICATION OF ELECTRIC SPINNING
Silk Fabrics with its soft and smooth feel, gorgeous appearance for people like
Electric Spinning is a kind of Silk Fabric, plain weave.
There are many kinds of power spinning, according to the different fabric materials, such as Silk Power Spinning, Viscose Silk Power Spinning, and Silk Viscose Silk Interwoven Power Spinning. According to the weight of the fabric per square meter, there are weight pounds (40g / M2 or more), medium, and Light Weight Pounds (20g / M2 or less). According to the different dyeing and finishing processes, there are whitening, whitening, dyeing, printing points. Power spinning products are often given ground names, such as Hanging (produced in Hangzhou). Shaofang Shanghai in Shaoxing) , Hufang (made in Huzhou) , etc. .
The Electric Textile material is close and fine and clean, the feeling is soft and firm, the luster is soft, the wearing is smooth and comfortable. The heavy ones are mainly used for summer shirts, skirts, and children’s clothing; the medium ones are used for lining; and the light ones are used for petticoats, headscarves, etc.
What’s yarn-dyed
Yarn-dyed fabrics — the Japanese term for “dyed fabrics” refers to the process of dyeing yarns or filaments before weaving them with colored yarns. This fabric is known as “dyed fabrics” and the factories that produce them are generally referred to as Dyeing Mills Denim, for example, and most shirt fabrics are dyed.
Because it is dyed before weaving, Dye permeability is strong, color weaving fastness is good, and color yarn fabric three-dimensional sense is a strong unique style.
Fabric Georgette knowledge, what is Georgette, and classification
(georgette)。
Georgette, also known as Georgette Crepe, is a strong twist crepe warp, Crepe weft weaving a silk fabric, Georgette’s name from France (Georgette).
Warp and WEFT are made of two kinds of strong yarns with different twist directions, S and Z, arranged in ZS and 2Z, interweaved in plain weave, the warp and weft density of the fabric is very
small. After being refined, the raw silk shrinks and crepes up due to the untwisting action of the silk thread, forming a Georgette with uniform crepe lines and loose structure.
According to the raw materials used, it can be divided into Silk Georgette, Rayon Georgette, Polyester Georgette Interwoven Georgette, etc. . If the WEFT is twisted in only one direction, it is woven into Georgette yarn, which is called CIS Fiber Georgette The cis-fiber Georgette shows irregular ruffles in the warp direction.
Georgette texture thin transparent, feel soft and elastic, the appearance of light and elegant, with good permeability and drape, wearing elegant, comfortable. Georgette’s light, weight, thickness, thickness, transparency, and CREPE shrinkage of the silk surface, mainly depends on the thickness of the Silk, the number of combinations, twist and warp, and weft density.
Georgette is suitable for making women’s dresses, high-end evening dresses, headscarves, palace lanterns, and other arts and crafts.
Identification and maintenance of SILK SCARF
IDENTIFICATION OF SILK:
1, satin-like all-silk fabrics have Pearl Luster, feel a little scraping hand feeling, chemical fiber fabrics shiny bright, harsh, feel stiff. Silk-like fabrics, though soft in the hand, are dull and without Pearl Luster.
2, Silk Fabrics, especially Silk Crepe de Chine, have a shrinkage of 8% to 10%, and the anti-crease performance is a little worse than chemical fiber, so it is claimed that no shrinkage, no-wrinkle silk should be more careful.
Silk Fiber is thin and long, cotton fiber is short, wool is curly, and chemical fiber is neat.
4. Silk Burns with a feathery smell and its ashes are fragile, Brittle, fluffy, and black, while Rayon (such as viscose) burns with a chemical smell of burning paper, while polyester burns with a
the slightly sweet smell and its ashes are hard and bead-shaped; Cotton and hemp burn have a burning paper smell, there is black-gray ash.
Maintain Silk:
Silk is a kind of protein fiber. The silk scarf knitted with silk has good ultraviolet absorption. Silk is a kind of porous fiber, so it has good properties of heat preservation, moisture absorption, moisture dispersion, and air permeability, and has a certain protective effect on the skin. Known as “human protein”, usually should pay attention to maintenance and collection, for your life to add lasting beautiful color.
1, Washing: Silk Clothing Best dry-cleaning, such as self-washing, should choose neutral detergent, in low-temperature water immersion 15 to 20 minutes, and then gently rub, and rinse with water, not suitable for washing machine, not suitable for alkaline soap, not suitable for high-temperature Washing Do Not knead vigorously. After washing to gently squeeze to moisture, and hang with the clothes rack, let it drip dry, to avoid sun exposure, to protect the color and luster after cleaning can put a basin of water, water drops into two or three drops of vinegar, Soak for 5 minutes, back to dry in the shade. Let dry to 80%. Iron when dry. Iron Silk Scarf, not high temperature, not directly iron, must be covered with a layer of wet white cotton cloth to iron again, in case of high temperature to make silk crisp or even scorch.
2. Storage: Don’t store silk scarves in damp or direct sunlight, which can cause mildew and discoloration. Avoid drying agents, cosmetics, perfume, and other direct contact with silk clothing. If inadvertently stained with, to timely cleaning, otherwise easy to become yellow or black. When stored, the utility model can be neatly folded and put in a drawer or can be hung on a smooth clothes rack, but it is not suitable to put camphor or sanitary balls, etc. . In addition, silk products in a long time, easy to harden, with a silk softener or white vinegar diluent immersion can restore softness.